ENGİNEERING
Using finite element method; strength, vibration and fatigue calculations can be made,
your designs can be improved in accordance with optimization efforts and weight
reduction studies are carried out without compromising strength.
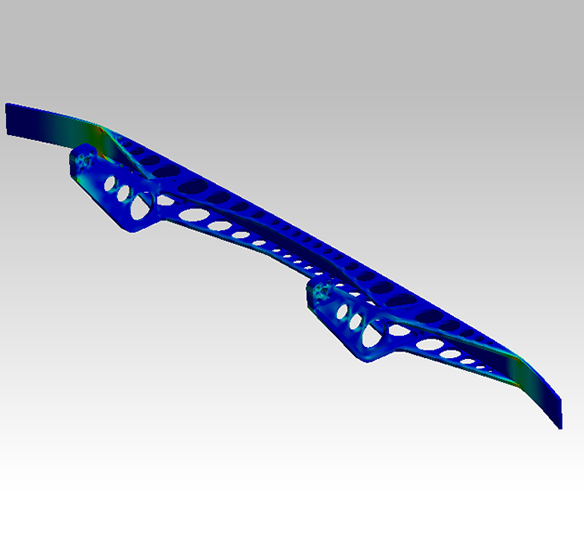
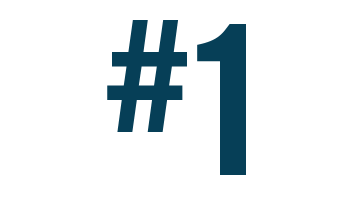
Topology Optimization
With the advancement of layered production technology, the old geometries have been replaced by topology optimizations with static and dynamic loads, high vibration damping capabilities during movement and reduced weight. It is aimed to minimize costs with these studies carried out in systems used in many sectors, especially in the defense industry. New designs or improvement works can be made and manufactured in accordance with your products, according to your wishes and in the light of necessary simulations.
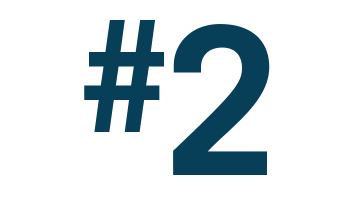
Dynamic
Parts subjected to static and dynamic loads and vibration effects on mechanical components such as chassis can be simulated and re-designed upon request.
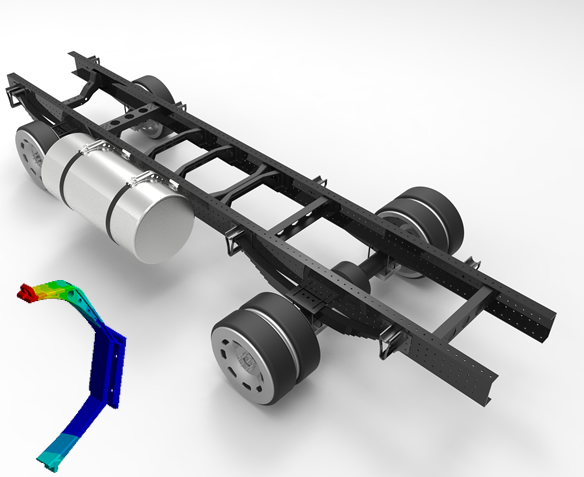
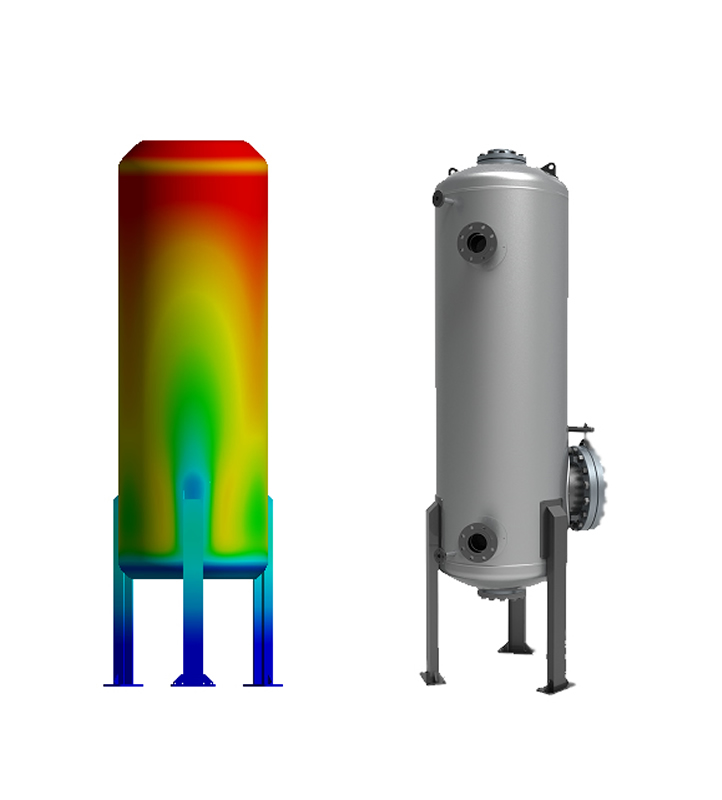
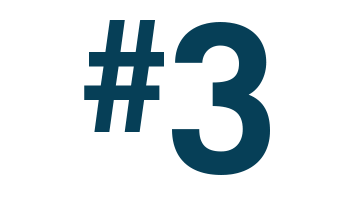
Pressure vessels
Pressure vessels are closed vessels designed to hold gases or liquids at a pressure that is substantially different from ambient pressure. Pressure vessels can be dangerous and historically, many fatal accidents have occurred due to pressure vessels. Consequently, pressure vessel design, production and operation should be carried out in accordance with standards. Storage tanks, reactors, heat exchangers have a wide range of applications such as hot water tanks used in homes, hospitals, industrial compressed air receivers, submarine and space applications, pneumatic reservoirs, diving tubes, autoclaves, petrochemical refineries. Because they operate at high temperatures and pressures, these temperature and pressure gradients can cause unpredictable high stresses in the connection areas and fatigue damage can occur during continuous operation.
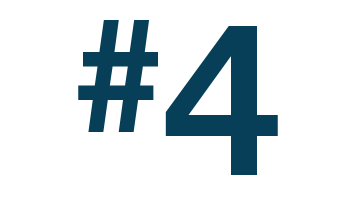
Fatigue
The continuous exposure of mechanical parts to external forces causes fatigue damage. ASGENA can perform fatigue analysis of your products in many sectors such as automotive, construction, maritime, energy sectors, especially in Aviation and Defense sectors and can reduce your costs by creating alternative designs when necessary.
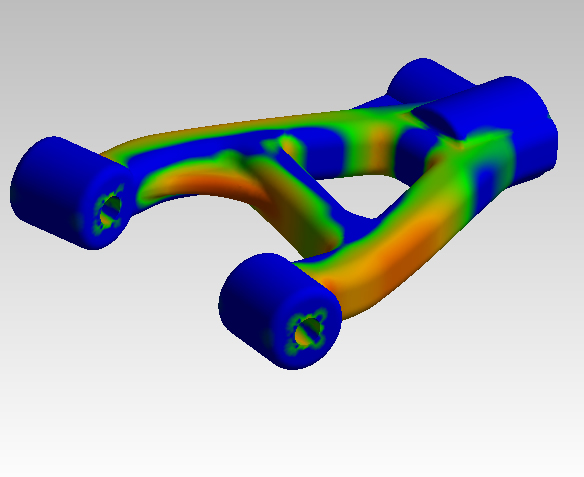
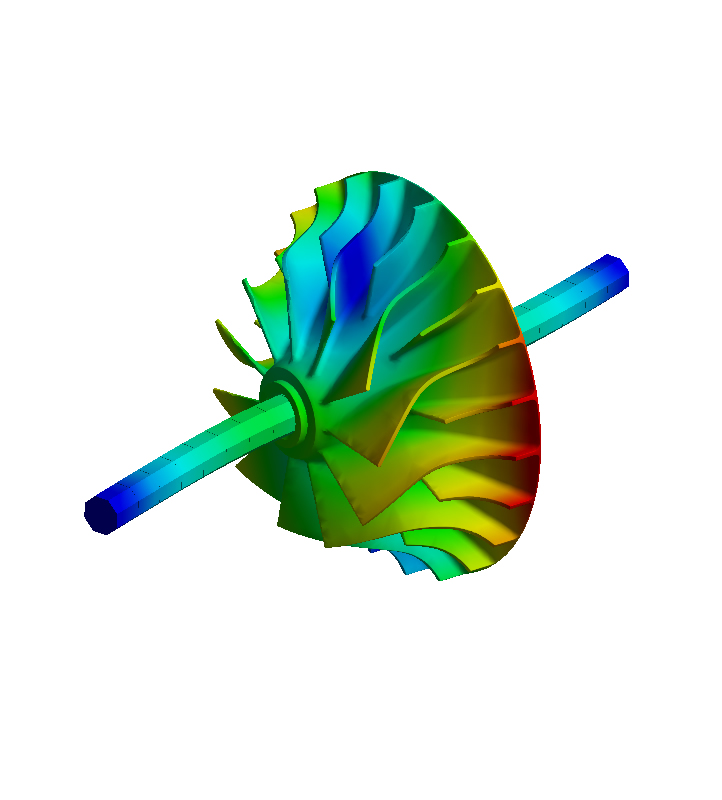
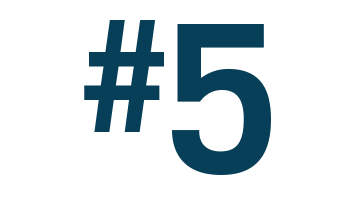
Vibration
Dynamic simulations are required to examine and analyze the behavior of rotating structures. As the rotational motion increases, the magnitude of the vibration reaches the maximum area called the critical speed. If the amplitude of vibration is excessive at these critical speeds, equipment loss, wear and tear on the machine, breakage beyond repair, and even loss of life may occur. As a result, there are imbalances that need to be corrected due to the internal structure and operating principle of turbo machines. The critical speed of a rotating machine occurs when the rotational speed matches the natural frequency of the natural machine. The lowest speed at which the natural frequency is first encountered is called the first critical speed, but as the speed increases, additional critical speeds will be seen. Therefore, minimizing rotating imbalance and unnecessary external forces is very important to reduce the general forces that initiate resonance. The finite element method approach can be used for modeling and analysis of the machine's natural frequencies, and the results can be verified with balancing machines.